FAQs
Have a question? Find answers to common queries about our sheet metal fabrication services, capabilities and processes. If you need more information, feel free to contact our team directly.
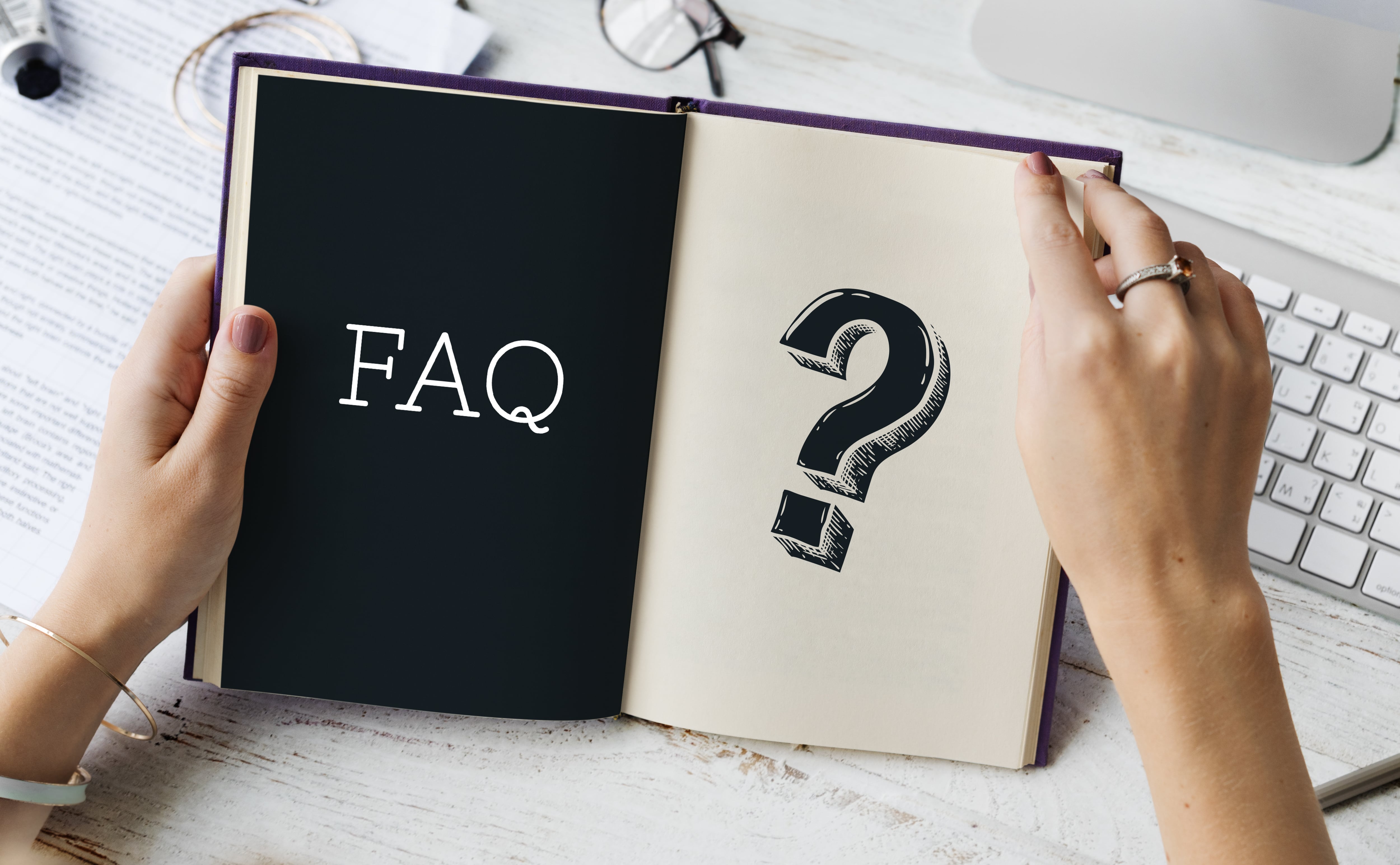
FAQ search
CNC machine tools are highly versatile, providing precision for a range of applications, including cutting, drilling, and forming metal. They can effortlessly cut materials like aluminium, stainless steel, and brass to exact specifications. For industrial applications, these tools are essential for drilling accurate holes in components used in automotive and aerospace manufacturing. Additionally, they excel in shaping metal for architectural purposes, such as creating durable roofing and complex structural elements.
Our laser cutting machines can cut the following materials; copper & brass, mild steel, stainless steel and aluminium.
We offer a number of products finishes to suit your project; galvanizing is our most popular one but we also offer zinc plating BZP, powder coating to Level 2 Qualicoat and chrome plating.
The thickness all depends on the material you decide to use, however copper & brass is the material with the least thickness whilst mild steel has the highest thickness.
Enhanced Accuracy - Customers receives highly precise cuts. Cost-Effective - Reduced material waste leads to lower production costs. Faster Turnaround - Quick, efficient cutting speeds up project timelines.Consistent Quality - Reliable, uniform results with minimal need for rework.
We aim for a 24hours turn around on all quotes.
We have our own fleet of delivery vehicles, allowing us to transport your products to any location nationwide. Delivery is available for an additional charge.
Lead times vary depending on the complexity and scale of the project. We work closely with our clients to establish realistic timelines and ensure timely delivery while maintaining high-quality standards.
Yes, we offer prototyping services to help you re-engineer your designs before full-scale production. This ensures that the final product meets the performance requirements.
Our facility is equipped with advanced, state-of-the-art machinery that enables us to scale production efficiently and meet large-volume demands. Additionally, being part of a group of companies, we have access to their facilities and equipment, providing us with the flexibility to expand capacity when needed. This ensures we can handle projects of any size, delivering consistent timely results.
Yes we do cater for smaller orders however we have a minimum order spend for each service; Laser only - 125 Laser/fold - 150 Laser, fold, fabrication, weld, paint - 400
Yes, we specialise in bespoke manufacturing with engineering advice on hand, tailoring your solutions to meet your specific requirements, whether for custom sizes, materials, or unique features to suit your product design.
At CEL, we adhere to the ISO 9001:2015 quality standard, ensuring that your products meet the highest levels of quality and reliability. You can trust us to deliver exceptional results, every time.
Our Radan design software supports various file formats, such as Inventor, SolidWorks, Catia (V4 & V5), SAT, IGES and STEP, making it easy to integrate with your existing design workflows.
The complexity of the enquiry depends on the lead time however estimates for each service are: from 24 hr laser cutting, from 72 laser/fold and from 2 weeks laser/fold/weld.
CEL Sheetmetlal, 11 Stafford Park, Telford, TF3 3AY
We serve all of the United Kingdom and have also supplied various European countries on projects
The typical lead time for a project depends on its complexity and scope. For laser cutting, the lead time is typically 3-5 days, while projects requiring laser folding usually take 5-10 days. Fully assembled products have a lead time of 4-6 weeks, with projects involving full engineering are typically completed within 6-8 weeks.
Yes, we provide both design and engineering assistance for projects. Our team works closely with clients to develop detailed designs, optimise for manufacturability, and ensure all engineering requirements are met to deliver high-quality results.
Yes, we specialise in handling complex and intricate designs. With our advanced equipment and experienced team, we can manufacture precise and detailed components while maintaining the highest quality standards.
Yes, we offer welding and finishing services to provide complete solutions for your projects. Our finishing services include powder coating, polishing, and other surface treatments to ensure your products meet both functional and aesthetic requirements.
We work with a wide range of sheet metal gauges and thicknesses to accommodate various project requirements, depending on the material and project specifications.
We calculate project costs based on several factors, including material type and quantity, the complexity of the design, processing requirements (such as cutting, folding, welding, and finishing), and lead times. Our team provides detailed quotes to ensure transparency and helps you find cost-effective solutions tailored to your project needs.
We accept a variety of payment methods to make the process convenient for our customers. These include pro forma, credit and debit cards, bank transfers and in some cases, business checks. If you have specific payment preferences or requirements, feel free to contact us, and we'll work to accommodate your needs.
Yes, we can ship products internationally. We work with reliable shipping partners to ensure safe and timely delivery to your location. Shipping costs and times will depend on the destination and size of the order, so please reach out to us for more specific information and to arrange logistics.
Still have questions?
Speak to a member of our team for further information, they are always happy to advise you on anything you're unsure on.