Exploring MIG, TIG, and Laser Welding: Which Is Right for You?
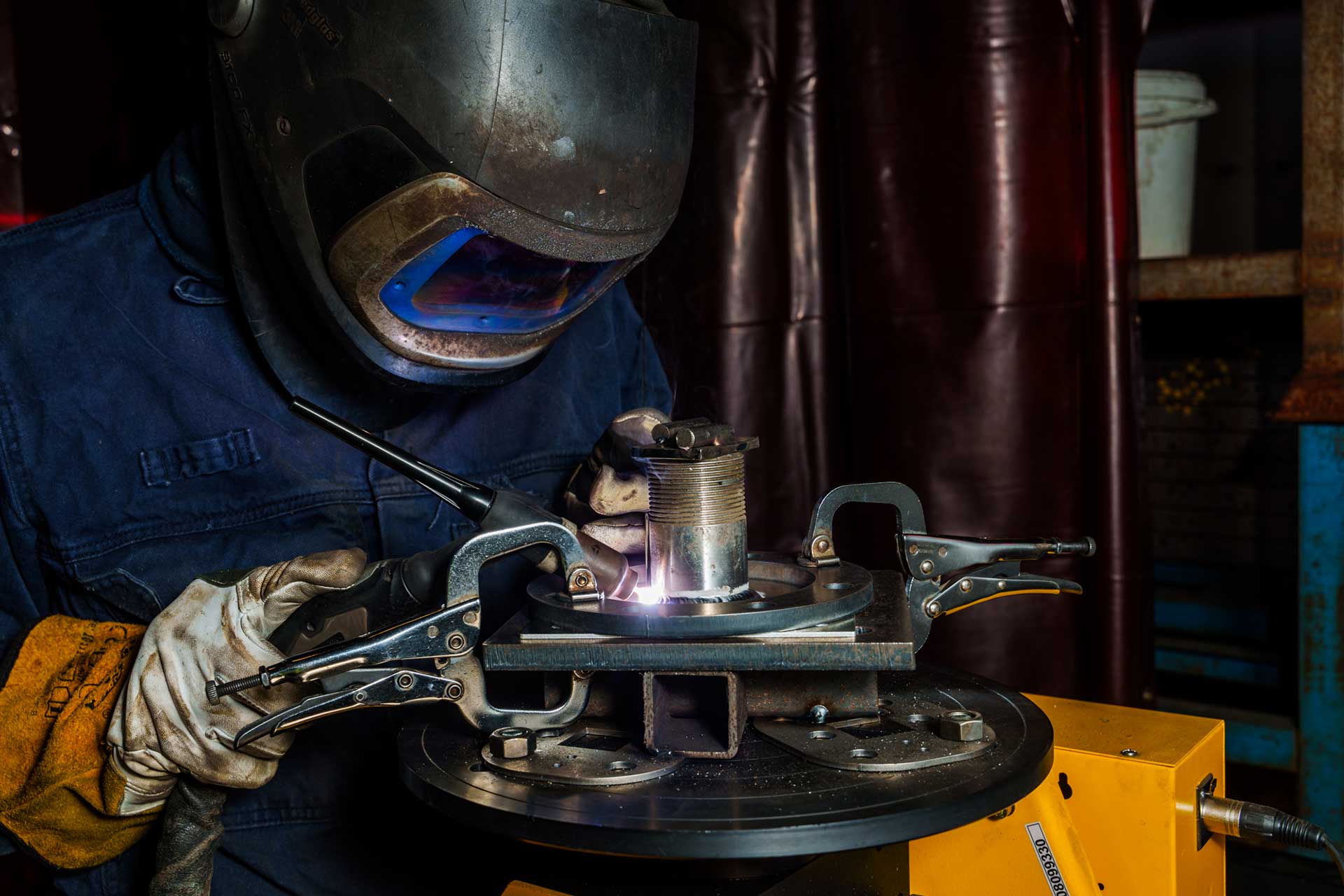
Welding is a fundamental process in metal fabrication, used to join metal parts for a variety of applications, from structural components to aesthetic finishes. The choice of welding technique plays a significant role in the overall strength, appearance and cost-effectiveness of a project. Three of the most commonly used methods—MIG, TIG and laser welding—each have unique characteristics that make them suitable for different types of work. Understanding these techniques will help you choose the best approach for your metal fabrication project.
MIG Welding (Metal Inert Gas Welding)
MIG welding, also known as Gas Metal Arc Welding (GMAW), is one of the most popular and versatile welding processes. This method uses a continuously fed wire that acts as both the electrode and filler material, which is melted to form the weld. The weld area is protected by a shielding gas, such as argon or CO2, to prevent contamination from the surrounding air.
MIG welding is ideal for projects that require high production rates, as it is a fast and efficient method. It is well-suited for welding thicker materials such as steel, stainless steel and aluminium. This process is perfect for automotive, construction and heavy machinery applications where speed and strength are essential.
One of the key advantages of MIG welding is that it is relatively easy to learn, making it a good choice for both beginners and experienced welders. However, it may not offer the same level of precision as TIG welding.
TIG Welding (Tungsten Inert Gas Welding)
TIG welding, or Gas Tungsten Arc Welding (GTAW), is known for its precision and high-quality welds. This method uses a non-consumable tungsten electrode to produce the weld and a separate filler rod is used if needed. Like MIG welding, TIG welding also uses an inert gas shield to protect the weld area.
TIG welding is best suited for applications that require detailed, high-quality work. It is commonly used in industries such as aerospace, automotive and artistic metalwork, where the appearance of the weld and the strength of the joint are critical. TIG welding provides excellent control over the weld pool, resulting in clean, smooth and aesthetically appealing welds with minimal spatter. It is perfect for welding thin materials like stainless steel, aluminium and magnesium and is the go-to option when precision and appearance are a priority. However, TIG welding is slower and requires more skill, making it less suitable for high-volume production compared to MIG welding.
Laser Welding
Laser welding utilises a high-powered laser beam to heat and melt the material at the joint, creating a weld. The focused laser energy allows for deep penetration with minimal heat-affected zones, making it a highly efficient and precise welding method. A shielding gas is used to prevent oxidation and contamination.
Laser welding is ideal for applications that require high precision and minimal thermal distortion. It is commonly used in the electronics, medical device and aerospace industries, where fine, delicate work is essential. This method allows for very narrow, deep welds that provide excellent strength while maintaining the integrity of surrounding materials. Additionally, laser welding can be automated, making it highly suitable for high-volume production. However, it requires specialized equipment and expertise and it is best suited for thin materials, as the laser beam may struggle to penetrate thicker materials effectively.
Choosing the Right Welding Technique
Selecting the appropriate welding method for your project depends on several factors, including the material you are working with, the precision required and your production needs.
For large-scale projects that require speed and efficiency, MIG welding is often the best choice. It is ideal for welding thicker materials and is suited for high-volume production. TIG welding, on the other hand, is the go-to option for precision work, offering superior control and quality, especially for thinner materials and applications where appearance matters. Laser welding is best when accuracy and speed are paramount, particularly in industries that require fine, precise welds on thin materials.
By understanding the unique benefits and limitations of each welding method, you can make an informed decision that aligns with your project’s specific requirements, ensuring that your metal fabrication project is both functional and aesthetically pleasing. Whether you're working on large construction projects, intricate aerospace components, or artistic designs, selecting the right welding technique will help ensure the success of your project.
Get your custom quote today
Ready to take the next step?
Contact us now for a tailored quote that meets your specific needs.